Blog
The Best-Kept Secret to Inventory Modeling that Captures Volatility
PUBLISHED ON:
March 31, 2023
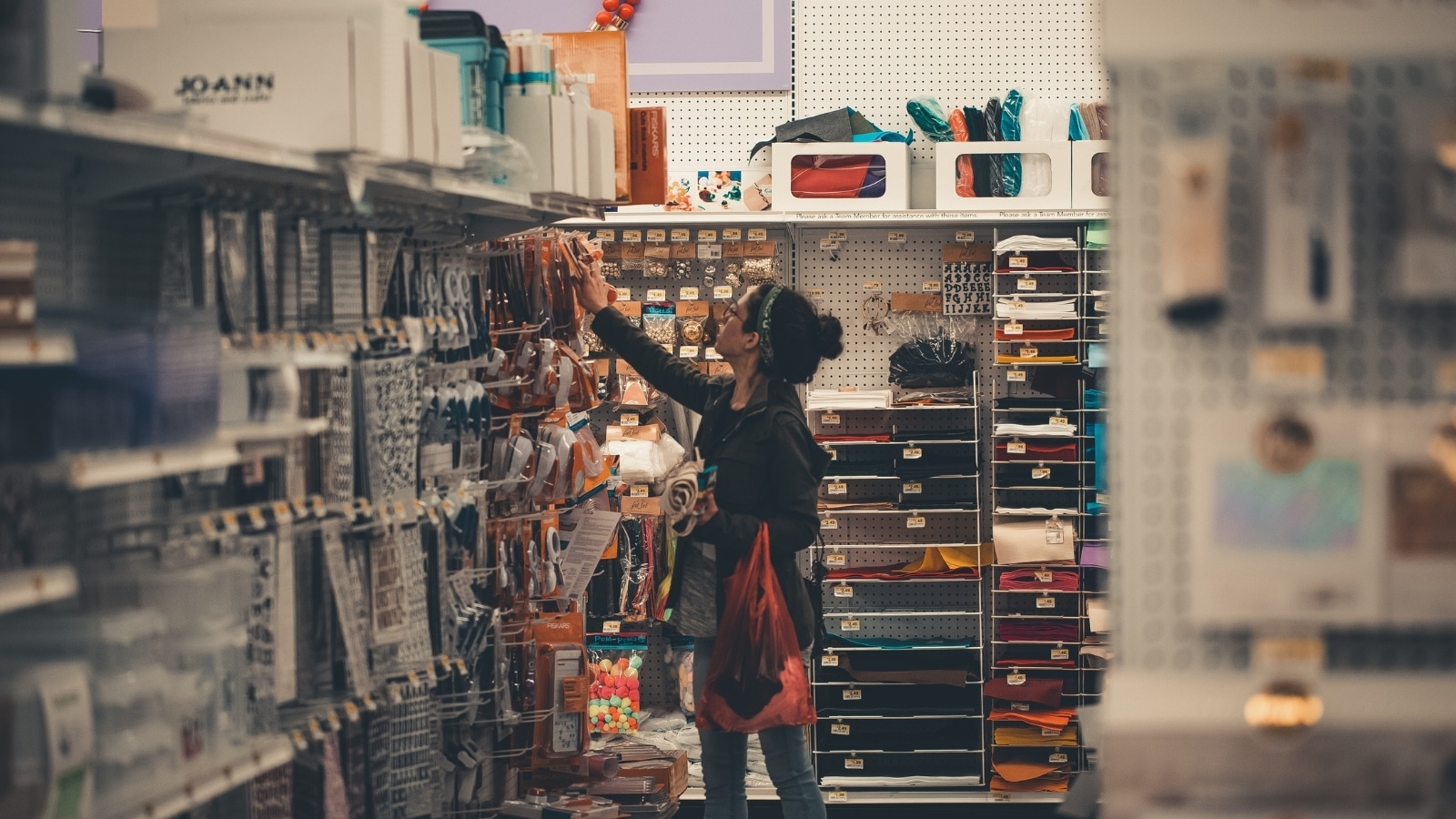
Subscribe to Receive the Latest Supply Chain Design Resources
Traditional optimization-only approaches to inventory planning fall short in the face of protracted uncertainty. Here’s why simulation is the best inventory management technology you never knew you needed.
Supply and Demand Uncertainty and Inventory Woes
The unpredictability of the past three years has proven—in devastating clarity—that yesterday’s planning methods are no longer sufficient to maintain healthy inventory levels.
Wild discrepancies between supply and demand resulted in a crazy roller coaster effect that vacillated between too much inventory and empty shelves. Retailers prepared for the worst and then were hit with demand they couldn’t match when consumers cashed their stimulus checks. And we all remember the now infamous Target inventory glut which resulted in brand damage and discounting that rivaled a garage sale.
In fact, according to IHL¹, inventory distortion (the annual cost of overstocks and out-of-stocks) has risen to $1.9 trillion in losses for retailers across the globe.
When asked about retail inventory strategy, John McQuiston, managing director and global head of originations, receivables and trade finance with Wells Fargo, said, “They’re guessing. They’re all guessing. And any one of them that tells you they’re not guessing, they’re lying, because they don’t know. The demand levels are entirely unpredictable. Consumer behavior is unpredictable.”²
It’s 2023, and uncertainty is here to stay. To be sure, businesses cannot afford to rely on inventory strategy based on guesswork and compete in today’s hyper-competitive market.
Why Does Traditional Inventory Management Fall Flat?
So why are some of the world’s arguably most advanced inventory technologies falling short when faced with today’s demand and supply volatility?
Multi-echelon complexity has increased exponentially with the globalization of consumers, reshoring, and the change in supplier base. Increasing and shifting fulfillment channels and nodes in the supply chain multiply complexity in ensuring the right inventory is in the right place at the right time.
Multi-echelon supply chains require a modeling approach that will account for the complexity and interdependencies of inventory decisions throughout the entire supply chain
Consumer expectations have evolved—not only do customers want fast delivery, but they expect a range of fulfillment choices as well, which further complicates inventory planning. For successful omnichannel fulfillment, reliable inventory management is crucial. When a store is out-of-stock for an item they planned to buy, 21% of consumers will leave and buy the item from a competitor store.³
Limitations of optimization-only technology: Optimization is the technology behind almost all the inventory management solution providers on the market today. The problem is, using only optimization is preventing companies from making accurate decisions around inventory because optimization uses abstraction around factors like demand, lead times, and capacity.
Because optimization uses abstraction around demand, lead times, and capacity, optimization-only solutions hinder accurate inventory decisions.
A combined optimization and simulation approach captures real-world variability affecting inventory.
Tackling post-COVID volatility requires planning techniques that consider all the variability that exists in demand, sourcing, transportation, and other factors when making inventory decisions.
Supply chain design opens a new approach to inventory optimization that combines simulation and optimization for a more accurate reflection of real-world volatility for healthier inventory.
Are you a bit in the dark when it comes to simulation? We’ve got you covered. Read on for a primer on simulation and why it’s the best complement to traditional inventory planning methods.
What Is Simulation?
Simulation is a modeling technique used to understand and predict the behavior of a system or process. Since it can closely represent real behaviors and conditions, simulation is often used to test potential changes to a system or to understand how a system will behave under new circumstances or disruptions.
Supply chains are complex systems with numerous interdependencies, and for certain types of supply chain analyses, this level of detail needs to be captured in the model to ensure a feasible, executable result.
Simulation captures real-world variability
Since most systems have some amount of inherent variability, a simulation model must be able to account for that variability to accurately represent the behavior. Variability might occur in demand, travel times, processing times, or quality specs, for example.
One the of many things we’ve learned over the past few years is the effect that outlier events and variation can have on a system: inventory outages and overages, bottlenecks, bullwhip effects, and more.
A simulation model that has stochastic (randomly determined) inputs will provide the user with a view into how variation affects all the complex interactions that exist in the supply chain.
Simulation shows performance over time
A simulation model is a dynamic model, which means that it can capture the performance of a system over time. Therefore, it captures the interactions and dependencies between different elements of the system.
Because the model is capturing events as they occur over time, the user can see how things such as inventory levels, storage capacity, and bottlenecks, for example, change throughout the model run. Allowing visibility into these details can unlock insights on system behavior that other modeling techniques cannot. This is why simulation is often referred to as a glass box, whereas static modeling, such as optimization, is a black box.
Simulation is often referred to as a “glass box” allowing the user to see how inventory levels, storage capacity, and bottlenecks change over time.
Simulation offers granular detail in models
Simulation allows for modeling at a more detailed level than other modeling techniques. Models typically contain more granular business rules, policies, capacity constraints, and production requirements, for example, than other modeling approaches.
Model inventory across the multiple tiers of your supply chain and capture the interdependencies between supplier inventory and each of your own inventory stocking locations throughout the network. Simulation models can capture the various details of demand, manufacturing cycle times, staffing requirements and transportation lead times; all of which can affect inventory strategy throughout the multi-tiered supply chain
This level of detail, along with the stochastic elements of the model, is one of the reasons that simulation modeling is a preferred method for service level analysis.
Taking the Guesswork Out of Inventory Planning with Simulation Optimization
We’ve shown that simulation can capture the variability and detail across a multi-tiered network that is needed to see how any given inventory policy and its parameters affect costs, service, and resiliency of the business. You might be thinking, “How do I determine which inventory policies and which parameters to put into the simulation model? I can’t possibly test hundreds of different combinations of policies, stocking levels, and reorder points.”
This is where simulation optimization is used. Simulation optimization seeks to optimize a specified fitness function that is based on the outputs of the simulation model.
In other words, simulation optimization seeks to find the best simulation scenario–or the best combination of simulation parameters–such as inventory policies, reorder points, etc. which optimize the specified function. It identifies the optimal inventory parameters by running numerous simulation scenarios. By combining optimization and simulation in this way, you can base inventory optimization and strategic planning on a more detailed, accurate representation of the system.
Combining optimization and simulation enables a more detailed, accurate approach to inventory optimization and strategy.
Advantages of Using Simulation for Inventory Planning
Why is simulation optimization so well suited for managing inventory strategy and policies? Here are a few of the most powerful reasons.
Inventory decision-making that includes accurate, detailed service level analysis
Inventory optimization isn’t only about choosing the most cost-effective solution; service levels cannot be compromised and therefore service level analysis is an incredibly important part of inventory optimization.
As we mentioned earlier, simulation allows for a more accurate level of service performance than traditional optimization modeling. These detailed service metrics, along with financial performance, can then be included in the search for the optimal scenario.
Simulation allows for a more accurate level of service performance than traditional optimization modeling.
Ability to model variability
The ability to model variability allows users to choose the correct inventory policy and targets that are created based on detailed, stochastic demand, not the simplified, aggregated demand that inventory optimization models use.
For example, variability in raw material arrivals that are part of the multi-tiered supply chain affect inventory planning strategies and therefore capturing this variability when setting inventory targets is critical.
Visibility into the “What” and the “Why”
Simulation provides both “what” and “why” whereas an optimization-only approach provides just the “what”. Simulation can be used to understand why one policy is better than another or why setting a target at a specific level is the right decision for the business. This instills trust in the model and provides the analyst with the ability to explain why they are recommending one solution over another.
Optimization simply provides the answer or recommendation without showing the user why it might be the best decision. Simulation also provides the “why”.
The analyst can also use simulation for insight into how a certain inventory policy will affect not only service levels, but also labor and fleet utilization, along with storage capacity. Optimization simply provides the answer or recommendation without showing the user why it might be the best decision. This is an example of why simulation is referred to as a glass box or in other words, a tool that provides visibility into what is happening in the system at any given moment.
New insights are often uncovered when an analyst can see inventory levels and movements change in the system over time.
Grow Your Knowledge
The 2025 CSCO Playbook: Leading with Influence, Speed, and Strategic Clarity
Discover how top CSCOs are leading in 2025 with influence, speed, and strategic clarity. This quick-read playbook reveals proven strategies to strengthen C-suite credibility, accelerate time-to-value, and build agile, resilient supply chains.
Lead Through the Shift: How Bold Supply Chain Design Turns Tariffs into Opportunity
Turn the new Trump tariffs into opportunity with supply chain design. Don’t wait for problems—use scenario planning for disruptions like tariff shocks, simulate possible outcomes, and create contingency playbooks to mitigate cost and risk.
Navigate Tariffs and Future Disruptions: Practical Steps for Supply Chain Executives
Discover how leading supply chain executives are proactively navigating tariffs and disruptions. Watch this on-demand webinar for practical steps, future-state scenario planning, and expert strategies to build long-term resilience.