Blog
Is Supply Chain Design for Mid-Market Companies Too?
PUBLISHED ON:
September 27, 2024
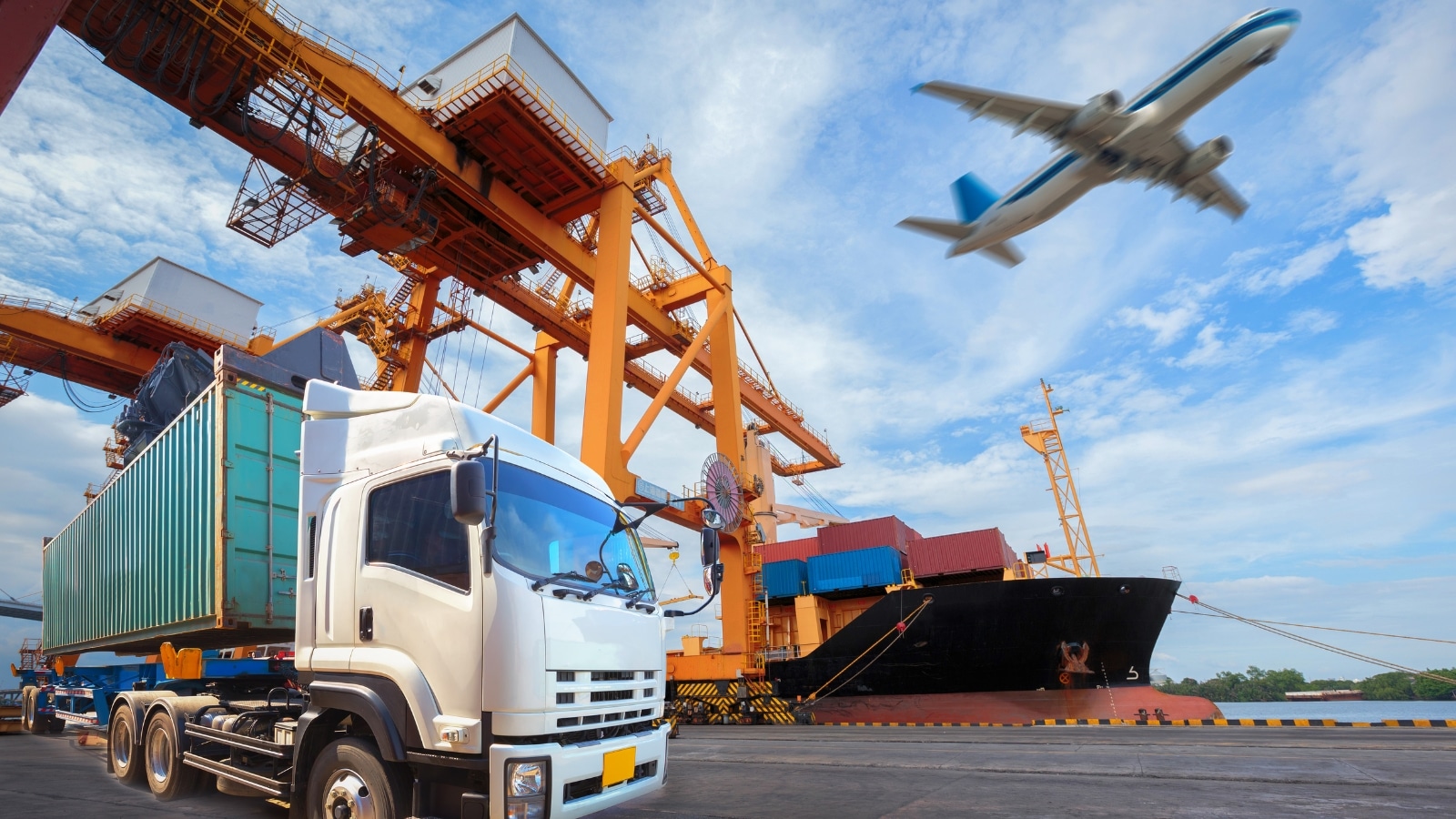
Subscribe to Receive the Latest Supply Chain Design Resources
By Jon Gilbert, Principal, Gilbert Sachs Group
When mid-market companies looking for help with supply chain design reach out to us, they are usually dealing with the same set of problems:
- Transportation and logistics operating costs are too high
- Too much working capital is tied up in the supply chain
- Customers want better service levels than the current system can provide
The truth is mid-market company supply chains (generally defined as between $100 million and $1 billion) can be every bit as complex and volatile as those of multi-billion-dollar companies. They grapple with many of the same challenges large companies face, plus, due to their size, they often have an extra hurdle to overcome—talent and staffing for supply chain design.
Here’s why supply chain design is crucial to the future success of mid-market companies in the manufacturing, retail, and distribution industries, and how these companies can take advantage of the same technology and benefits as their Fortune 500 counterparts.
What Is Supply Chain Design?
Supply chain design is the process of creating digital models of your future-state supply chain to accurately predict the performance of each design in terms of service, financials, and risk.
Supply chain design can explore every type of decision regarding the structure and policies of your supply chain, such as:
- How many facilities should we have and where should they be located?
- Which SKUs should be stocked and where?
- How can we better plan and deploy our inventories?
- What mode(s) of transportation should we use in each lane?
- What should we do about our suppliers?
- How should we invest in our supply chain?
Why Is Design Crucial to Midmarket Success?
No matter how effective your supply chain planning is, you’ll never do better than the supply chain’s design allows you to be.
Supply chain design is how you change and improve the entire supply chain system, as Don Hicks, CEO at Optilogic says, you “shift the efficiency frontier”. A supply chain that is poorly designed—or has evolved to be out of step with the environment—limits how optimal your supply chain planning processes will be. With a better design, your best planning decisions can get even better.
For example, we recently worked with a mid-market CPG (consumer packaged goods) shipper struggling to efficiently serve large grocery store and warehouse club customers. Modeling their supply chain showed that moving production of a few SKUs, establishing a DC closer to demand, and changing the way they scheduled could yield distribution and outbound transportation savings approaching 10%. They had thought about making these changes for years but lacked the internal resources and skills needed to take on the project.
The Talent and Staffing Problem
Designing and redesigning the supply chain requires decisions about what’s most important: the team must weigh the trade-offs across financials, service, risk, and sustainability and decide which design will best support the enterprise’s long-term objectives.
That kind of decision can’t be automated, and it can’t be done by an AI bot.
This means that the human designer is crucial to success in supply chain design. Mid-market companies are usually not big enough to have a dedicated supply chain design team. That just means they need help.
Why Mid-Market Focused Consultancies are a Perfect Match
Without much depth of staff, the most senior supply chain manager is often the only resource in the company capable of doing the work; and they are usually extremely busy with other aspects of their job. Sound familiar?
Mid-market focused consultancies understand these constraints of budget, time, and resources at your company, and bring a pragmatic and efficient approach to delivering supply chain improvements. With the careful application of consulting support, we can provide a turnkey solution to accomplish this task affordably, without overextending your internal resources.
Design Is for “Big Bang” Changes to Tiny Operational Changes
Many people mistakenly believe supply chain design is just about “big bang” projects like moving facilities and changing suppliers. But design doesn’t have to be a wholesale change and many design recommendations can be implemented without major disruption to the business.
Supply chain design is also for evaluating things like changing which SKUs are stocked in which location, different transportation modes, frequencies of replenishment, and other updates.
Supply chain design is about changing supply chain structure and policies and detailed business rules. You can evaluate any potential changes to the supply chain: from the biggest to the tiniest operational changes.
Delivering Value from Optimization at Your Company
So how do we deliver value to your stakeholders from optimization? Just like completing a journey of a thousand miles, we do it one step at a time.
- First, we work with you to set the destination; determining what questions to answer, what to optimize, and specifically how the findings will deliver benefits.
- We then translate your needs and questions directly into the Cosmic Frog model and scenarios to test.
- While all this is happening, we gather detailed data on your inbound and outbound movements, inventories, costs, service requirements, and other relevant data
- Next, we load the data and begin testing the model, making sure that it is generating trustworthy output and providing definitive answers.
- Through a series of conversations with you, we refine the data and inputs, adjust the model, and develop initial findings.
- Findings are shared and further refined, and the final output is created
- All through this process, groundwork for future re-optimizations is laid, providing a path for future adjustments to your business that can be made quickly, more frequently, and at minimal cost.
Mid-market companies we work with that optimize their supply chains often realize savings of 5% to 10%, and sometimes much more. And all of the savings go directly to EBITDA. What benefits could your company realize?
Jon Gilbert, Founder and Principal of Gilbert Sachs Group, is an expert in optimizing transportation and logistics, supply chain management, and planning. He has over 30 years of experience in improving service, building revenue, increasing efficiency, and integrating new technologies in diverse industries. Connect with me on LinkedIn.